![]()
Photocoupler
High-precision spectrophotometer for measuring spectral transmittance
Key words: high-precision spectrophotometer; transmittance; US instrumentation ; UV-1100; UV-1800
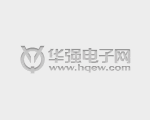
This model of UV spectrophotometer system features a fully automated single beam measuring instrument based on a dual grating monochromator. An integrating sphere is introduced in the exiting optical path to eliminate the polarization and non-uniformity of the beam, and in the signal receiving part, the filter and the detector are considered as a whole, and the advantage is that the actual use environment of the filter is close. , reducing its actual measurement error. The design process and uncertainty analysis of the instrument are highlighted. Sources of uncertainty for measurement include source stability, dual monochromator repeatability, reproducibility, beam uniformity, internal reflection, detector linearity, stability, polarization, uniformity, system stray light. The uncertainty of the transmittance of the filter measured by the instrument is 5.859×10-3, which fully meets the measurement accuracy requirements. Dual beam UV spectrophotometer UV-1800. Introduction At present, in the field of optical remote sensing sensor calibration, the filter radiometer based on silicon trap detector is an effective way to solve the high-precision radiation calibration of band-type instruments. Because of its small size, light weight and low power consumption, it is in the field. It has broad application prospects in airborne and spaceborne high-precision radiometric calibration. Therefore, measurement of filter transmittance and absolute response of the detector is critical to improving the measurement accuracy of the filter radiometer. Dual beam UV spectrophotometer UV-1800. It is proved by experiments that the absolute spectral response rate uncertainty of the silicon trap detector is less than 0.035%, which can be used as a high-precision absolute spectral response rate standard detector. The uncertainty of the filter transmittance becomes filter radiation. The main source of measurement uncertainty. Although many commercial instruments measure transmittance relatively accurately, it is difficult to estimate the system uncertainty introduced by various instrument parameters. The high-precision spectrophotometer is based on the dk242 dual monochromator and is designed with an incident light path and an outgoing light path. The incident optical path is composed of two off-axis parabolic mirrors and a light source cooling system, and the exiting optical path mainly includes an off-axis parabolic mirror and an integrating sphere. Because the beam emitted by the monochromator has a distinct filament image, the integrating sphere primarily acts as a uniform dual monochromator to emit light and eliminate the polarization of monochromatic light. The receiving part directly adopts the filter radiometer as the detecting unit, because it is difficult to ensure that the beam incident on the surface of the filter is parallel light in actual measurement, and the spectral transmittance curve and the angle of the incident light also have a great relationship. Taking the filter and detector as a whole is beneficial to the measured spectral transmittance being closer to the actual measurement conditions. The optical path of the whole instrument adopts single optical path instead of dual optical path mainly because: First, the single optical path has larger luminous flux than the double optical path, and the optical path adjustment is simple; secondly, reducing the error introduced by the system is beneficial to the analysis of the uncertainty of the instrument. The biggest characteristic of the dual monochromator is that the light intensity is very weak, and the intensity of the emitted light is reduced by about 100 times after being homogenized by the integrating sphere, so that the signal-to-noise ratio of the detector is very low, which is close to the noise floor of the detector. Dual beam UV spectrophotometer UV-1800. In order to solve the contradiction of low signal-to-noise ratio, a lock-in amplifier is added at the exit slit of the dual monochromator, thereby improving the signal-to-noise ratio of the detector and providing a guarantee for improving the measurement accuracy. The high-precision spectrophotometer based on the dual monochromator has a composite uncertainty of 5.958×10-3 for the spectral transmittance measurement of the filter. Therefore, the spectral transmittance measured by the instrument can be directly applied to the actual measurement of the filter radiometer, establishing a high connection between the transfer standard (trap detector) and the working standard (integral sphere calibration source and standard lamp, etc.) Accuracy radiation standard transfer relationship, high-precision measurement of radiation such as spectral radiance and spectral irradiance. Dual-beam UV spectrophotometer UV-1800. 1 High-precision spectrophotometer system composition 1.1 What kind of optical structure is used in the illumination part of the incident light path, which has a great influence on the incident efficiency of the system and the subsequent exit efficiency. In the selection of optical structure, the following methods are mainly considered: 1.1.1 The first lens of the double lens type is collimated, the filament is placed at the focus, and after the first lens, it becomes parallel light; the second The lens is designed according to the system's f# and focuses the parallel light to the entrance slit. The structure has the advantages of simple structure and high utilization of light energy. Its disadvantage is that due to the use of the lens, it is indispensable to introduce aberrations such as chromatic aberration and spherical aberration into the system, which is a serious problem for the spectrum test system. 1.1.2 Fiber Introduction Mode Fiber bundles consisting of multiple fibers are usually used here. One end couples the light from the source into the fiber through the coupling device, and the other end arranges the fibers into the shape of the entrance slit. Fiber optic selection takes into account the f# match with the monochromator. The significant advantages of this method are: simple structure and convenient use. At the same time, there are also shortcomings: the optical fiber has transmission loss, the emission efficiency is not high, the output is unstable, and the cooperation of the optical fiber and the slit has high requirements for mechanical adjustment, and it is difficult to ensure high-precision coupling repeatability. Obviously, its shortcomings are unacceptable for calibration test systems. 1.1.3 Double Parabolic Mirror Parabolic mirrors have the following characteristics: for rays coming from the focus, they are emitted parallel through the parabolic mirror; for parallel incident rays, they are concentrated by the parabolic mirror to the focus. This illumination method uses a pair of identical off-axis parabolic mirrors. The light source is located at the focus of the first mirror. After the first specular reflection, parallel light is formed and transmitted to the second mirror. The parallel light is emitted. The direction is parallel to the optical axis of the parabolic mirror, and the second parabolic mirror concentrates the light at the focal point, which is the entrance slit of the monochromator. The advantage of this method is that a reflective structure is adopted in the optical path, no aberration is introduced, and the efficiency is high; the disadvantage is that since the off-axis parabolic mirror belongs to an aspherical mirror, the processing is difficult and the cost is high. Comprehensively comparing the advantages and disadvantages of these three methods, we chose the third. This is mainly determined according to our usage requirements. In practice, the range of the spectrum covered by the monochromator is wide. If the lens system is used, the beam path will inevitably have a large deviation during the band change, and the test conditions will change. In addition, the energy required to be as stable as possible during the test is difficult to ensure with fiber optic systems. The third way, except for the complicated processing, has no obvious shortcomings and is finally applied to the system. We chose the dk242 dual monochromator. Since the dk-242 dual monochromator is a series of two identical monochromators, it has two modes of operation: plus or minus. Usually, the dual monochromator operates in the plus mode and works in the plus mode. The two gratings rotate in the same direction and angle. The light emitted by the first monochromator is emitted by the second grating and is again dispersed. This is equivalent to a twofold increase in focal length and a twofold increase in spectral resolution of the system. At the same time, in the dual monochromator, each optical path has a corresponding aperture limitation, and the spacers are treated by a special process to minimize the reflection of light, so that the stray light in the emitted light is less than 10-10. The dk-242 uses a concave mirror focusing and collimating czerny-turner structure in the design. The grating is placed on a triangular turntable, and each side is fixed with a grating. By properly selecting the grating configuration, the spectrum coverage of the monochromator can fully meet the user's requirements. In use, the stepper motor is driven, and the grating used is selected by software, and the turntable is rotated to a predetermined position. Since the three sets of gratings in the dual monochromator have different parameters and different spectral coverage, the spectral resolution that can be provided is also different. 1.3 Ejecting light path The dual monochromator exit beam is characterized by a large divergence angle, with light and dark stripes (because the outgoing beam becomes a filament image), and because the dual monochromator exit slit is very small (for example, when the resolution is 0.75 nm, Then the exit slit is only about 220μm. The light energy distribution at the edge of the beam is not uniform. If it is directly incident on the detector, it will inevitably cause a large error in measurement. Therefore, the integration of the integrating sphere must be performed before the detector is received, so that the detector receives a uniform spot, which is also similar to the actual measurement conditions. Since the beam image is close to the exit slit, if the integrating sphere is directly added to the exit pupil of the dual monochromator, although the optical path is very compact, the mechanical repeatability is poor, and it is not possible to clearly judge that the beam is completely incident on the integrating sphere. The author is inspired by the incident light path and is imaged at the entrance of the integrating sphere by two off-axis parabolic mirrors, which not only makes it easy to adjust the beam into the integrating sphere, but more importantly, it can be added to the exit pupil of the dual monochromator. The waver satisfies the principle that the modulation position is better at the front end of the system (the incident light path and the double monochromator are matched by f#, and the chopper cannot be inserted, so it is placed in the outgoing light path). Another characteristic of the dual monochromator is that the emitted light is very weak. If the light is further attenuated by nearly 100 times, the measured signal and the detector's noise floor are very close, and the signal-to-noise ratio is very low. An optical chopper and a lock-in amplifier are added to the optical path to increase the signal-to-noise ratio of the detector so that the measurement accuracy meets the requirements. 2 Parameter design of each part of the optical path 2.1 Working principle The high-precision spectrophotometer system consists of the incident and outgoing optical paths, the dual monochromator, the chopper, the integrating sphere, the lock-in amplifier, etc. The working principle diagram is shown in Fig. 3. The beam emitted by the tungsten halogen lamp is incident on the voltage monitoring circuit through a part of the splitting piece, and the other part is imaged by the two off-axis parabolic mirrors of the incident optical path to the incident slit of the double monochromator through the double monochromator. The splitting light enters the incident optical path after being chopped by the chopper, and is finally received by the filter radiometer. The detector converts the modulated light energy into an alternating current signal, and the signal processing circuit of the lock-in amplifier amplifies and shapes the alternating current signal. The filtering process becomes the corresponding DC signal and is finally uploaded to the PC via the gpib interface. Dual beam UV spectrophotometer UV-1800. From the working principle, this measurement filter transmittance is a method of spectrally scanning the filter band by a dual monochromator. Generally, the spectral transmittance is usually defined as the ratio of transmitted light to incident light, if is the measured value when the filter is loaded, iuf is the measured value when the filter is not loaded, and i0 is the measured value of the detector background noise. Before the test, the noise floor of the detector is measured first, then the detector values ​​under the condition of loading and unloading the filter are measured in turn, and the transmittance value at the corresponding wavelength is obtained by using the transmittance definition formula. Finally, the software is used to compensate the measured values ​​for the fluctuation of the light source, which makes it possible to measure the transmittance of the filter with high precision. 2.2 Determination of optical path parameters The optical path design is mainly designed around the parameters of the dual monochromator. According to the characteristics of the emitted light, some main parameters of the incident optical path and the outgoing optical path are estimated. 2.2.1 Incident path parameters The incident path requires that the beam emerging from the source be incident on the monochromator to the maximum extent possible. According to this design idea, an off-axis parabolic mirror is used in the optical path, and the size is designed according to the f# of the double monochromator, the mirror size is 61 mm×61 mm, and the focal length is 240 mm. A heat sink is added to both sides of the light source so that the heat around the light source does not gather, thereby ensuring the stability of the light source. In order to quantitatively evaluate the stability of the light source and correct it in subsequent measurements, a high-precision trap detector is inserted into the incident light path to monitor the stability of the light source, which provides a basis for the correction of the spectral transmittance. 2.2.2 Double Monochromator Parameter Design The dual monochromator parameters are mainly based on the required measurement resolution to select the width of the entrance slit and the exit slit, and the scan speed is selected according to the signal to noise ratio of the dual monochromator. The entrance slit and the exit slit width are calculated according to the grating equation and the selected spectral position, and the current line dispersion coefficient is calculated, and then the width of the slit is calculated and adjusted to the corresponding position by the user selected spectral resolution. . The grating equation is as follows: λ is the wavelength, θ is the angle between the incident light and the normal of the grating, which is half the angle between the incident light and the current spectral light, and d is the grating constant. According to the wavelength range of the filter transmission, the selected grating is 1200 lines/mm. It is known that 2φ is 15o, and it can be found that θ is 25.113o at this time. According to the formula for calculating the dispersion coefficient of the grating line, there are: where d and dθ are respectively the line dispersion power and the role dispersion. When deriving the two sides of the grating equation simultaneously, it can be obtained that when the dk-242 is operated in the additive mode, the focal length should be the sum of the two focal lengths, that is, 480 mm. From the above formula, the reciprocal of the line dispersion coefficient at the corresponding wavelength can be calculated. According to the relationship between the wavelength resolution and the reciprocal of the exit slit and the line dispersion coefficient: the width of the double monochromator exit slit and the incident slit at the corresponding wavelength is calculated by the equation (4). For the scanning speed, it directly affects the signal-to-noise ratio measured by the dual monochromator. The relationship between the spectral scanning speed r and the signal-to-noise ratio is δγ is the slit-related resolution, and r is the spectral scanning speed. It can be seen from the formula that if the resolution of the dual monochromator is required to be increased, or the scanning speed is fast, the signal-to-noise ratio of the monochromator must be lowered, so that the scanning speed is selected to be 100 nm/min while taking into consideration the measurement time. 2.2.3 Outlet optical path parameter design The beam emitted by the dual monochromator is characterized by weak energy, uneven beam, and polarization. According to this characteristic, an integrating sphere and a lock-in amplifier are added to the exiting optical path, the integrating sphere acts as a uniform beam and depolarization, and the lock-in amplifier functions to detect a weak signal. The design of the integrating sphere is based on the light source used, the size of the spot emitted by the dual monochromator, and the subsequent detector design. Its design is very important, not only related to the uniformity of the outgoing spot, but also related to how much modulation frequency the optical chopper needs to set to meet the signal-to-noise ratio of the detector. First, it is necessary to estimate the radiance value of the light source, and use the Planck formula to obtain the irradiance of the light source, which is converted into radiance. Secondly, the reflection efficiency of each mirror inside the dual monochromator is calculated, and the radiation flux of the outgoing beam is obtained. Finally, the integrator sphere exit brightness is calculated by passing the integral sphere brightness formula: a is the inner surface area of ​​the integrating sphere. f is the aperture ratio of the integrating sphere, and Ï is the integral sphere reflectivity, taking Ï=0.97. Through calculation, some parameters such as the brightness of the output beam of the integrating sphere, the size of the integrating sphere, the area of ​​the inlet and the outlet are obtained. In this experiment, the integrating sphere has a diameter of 30 mm and the material is f4. The inlet is designed to have a rectangular shape of 2 mm × 4 mm according to the shape of the outgoing beam, and the shape of the outlet is designed as a circle having a diameter of 8 mm according to the angle of view of the rear detector and its effective receiving surface. Since the light energy emitted from the integrating sphere is very weak (10-7 orders), it is almost annihilated by the noise of the detector and subsequent circuits. Therefore, a chopper is added to the exit path of the dual monochromator, usually the chopping frequency is higher. Larger, the more favorable it is to extract the effective signal in the noise. Through experiments, the chopping frequency was chosen to be 1 khz. 2.2.4 Detector part design Usually the measuring unit is combined with the integrating sphere and detector in the signal receiving part, but the actual measuring condition of the filter radiometer is taken into account in the design of the instrument, that is, the beam may not be in actual measurement. Normal incidence, but incident at a certain angle of incidence, so that the measured irradiance has a large error with the actual value (mainly the filter transmittance varies with the angle of incidence). The filter and the detector are used as the measuring unit, and the light emitted from the integrating sphere is directly irradiated to the detector. This irradiation mode is similar to the actual measurement state of the filter radiometer, so the measured filter transmittance is more consistent. The actual measurement conditions can be directly used for the filter radiometer without the need to correct the filter transmittance in subsequent data processing. In addition, since the detector portion uses a light trap detector with a reflectivity of 0.25%, the internal reflection between it and the filter is negligible. 3 Measurement experiment and instrument uncertainty analysis 3.1 Measurement process The system is preheated for 30~40 minutes before the measurement experiment, including lamp, integrating sphere and detector preheating. The optical path can be adjusted while preheating. The optical path adjustment is mainly to ensure that the spot incident on the dual monochromator can fill the grating to maximize the grating efficiency, and at the same time adjust the integrating sphere and the filter radiometer in the exiting optical path to make them On the same optical axis. In order to ensure the accuracy of the measured value, on the one hand, the light source monitoring circuit records the fluctuation data of the light source. On the one hand, since the center wavelength of the filter changes with the temperature, the temperature generally rises, the center wavelength shifts to the long wave direction, and the temperature decreases. Otherwise vice versa. Therefore, a temperature measuring device is also added to the subsequent exiting optical path. By monitoring external disturbances through these two aspects, the measurement data is corrected in time. The entrance slit and the exit slit width of the dual monochromator are set according to the resolution required for the measurement and the filter band, and the general slit width is set to be constant during the measurement. When the dual monochromator scans the spectrum, it controls its operation through its own software. When it reaches the specified wavelength, it starts the collector to collect the data. In order to ensure the reliability of the data, it is generally measured 10 times at the same wavelength, and then the average value is taken as the wavelength. Lower measured value. When the collector has finished collecting data, start the dual monochromator to the next band. The above process is repeated in turn until the measurement ends. It takes about 50 minutes to change the spectral transmittance formula at the corresponding wavelength to a single optical path to measure the primary spectral transmittance, which is mainly determined by the time at which data is collected at a single wavelength. 3.2 Instrument Uncertainty Analysis The uncertainty source of the filter transmittance curve is mainly derived from the three parts of the incident optical path, the dual monochromator and the outgoing optical path (see Table 1). The uncertainty included in the measurement results is caused by the following factors: 3.2.1 Power supply for the light source The system light source uses a high-power constant current source and is monitored by the monitoring circuit. The power source power fluctuation caused by the power supply is less than 0.1‰. 3.2.2 Double monochromator system Partial repeatability and reproducibility The optical device that participates in changing the optical path inside the dual monochromator system has 12 mirrors and two gratings. Due to the influence of air humidity and dust, it is inevitable. It will reduce their reflection and diffraction efficiency, thus affecting the output stability of the system. In addition, the dual monochromator spectrum selection is to drive the worm gear through the stepper motor to rotate the grating on the grating table, which makes the sinusoidal motion required in the grating equation become linear motion. There is a gap between the stepping motor and the worm gear, which will directly lead to the inaccuracy of the position of the outgoing spectrum and affect the accuracy of the system output. The influence of these two error sources on the emitted light of the system can be obtained from the nominal value of the factory of the dual monochromator: the double monochromator has a nominal stray light <10-10, so the item can be ignored; The maximum deviation of the spectral precision and accuracy of the instrument is 0.07 nm, and the resulting response rate change is about 3.1 ‰ (according to the detector linear fitting equation). The repeatability of the double monochromator was 4.9 ç» and the reproducibility was 3.1 ç». 3.3 Low-temperature radiometer calibration trap detector absolute spectral response rate In the experiment, seven single-wavelength lasers were used as the light source, the wavelengths were 488nm, 514nm, 594nm, 633nm, 676nm, 786nm, 830nm, 944nm. The spectral response values ​​of ten power points were measured at 25 μW intervals for each wavelength in the range of 25 to 250 μW. Detailed calibration process reference [1]. It is known from reference [1] that the absolute spectral response rate of the trap detector is less than 0.035%. 3.4 Trap detector stability, polarization sensitivity, linearity and spatial uniformity 3.4.1 Trap detection stability After sufficient warm-up, the trap detector is continuously operated for 8h, and its output voltage is collected every 30s. After the ratio of the laser power is removed by the ratio of the two optical paths, the root mean square fluctuation of the detector itself is 0.00678%. Long-term (months to years) stability of trap detectors is ensured by periodic calibration with a cryoradiometer. 3.4.2 Trap detector polarization sensitivity causes the trap detector to rotate 360° relative to the incident optical axis, measuring its output voltage every 30° with a root mean square fluctuation of 0.00492%. 3.4.3 Trap detector linear trap detector linear measurement is tested by superposition method, that is, the basic principle is that two luminous fluxes Ñ„1 and Ñ„2 generated by two light sources are respectively irradiated on the detector to generate two corresponding responses. N1 and n2. The two luminous fluxes Ñ„1+Ñ„2 are then simultaneously illuminated on the detector, producing a response n12. If n1+n2=n12, then the detector is linear. If n1+n2≠n12, then the degree of deviation from linearity can be described by a nonlinear factor, which is defined as: (/()) 11212nl = nn+n. The linear uncertainty of the trap detector measured by this method is 0.073%. 3.4.4 Trap Detector Spatial uniformity allows the trap detector to translate in steps of 0.5 mm perpendicular to the x, y direction of the incident beam while measuring its output voltage. When the translation range of the trap detector relative to the center of the incident aperture is x, y = -2~2mm, the root mean square fluctuation of the response is 0.0199%. 3.5 Beam uniformity Since the light emitted from the dual monochromator has light and dark stripes, it is bound to cause a large error if it is directly incident on the detector. Therefore, the beam emerging from the dual monochromator must enter the integrating sphere to be homogenized. In order to evaluate the uniformity of the light emitted by the integrating sphere, the authors used a detection system that measures the uniformity of the sphere of the small-diameter integral to detect the integrating sphere used in the system. The system uses lens imaging for indirect detection, and uses computer controlled scanning to analyze and process the data collected by the high-precision standard detector to obtain the uniformity of the surface of the integrating sphere. The integrating sphere uniformity in the system was tested to be 99.658%. 3.6 Internal reflection of the beam For self-designed high-precision spectrophotometers, the internal reflection mainly occurs between the exit of the dual monochromator and the filter, between the integrating sphere and the filter, as well as in the filter and detection. Between the devices. Through theoretical analysis, between the filter and the detector, since the detector uses a trap detector, almost all of the light beam incident on the detector is absorbed by the detector, so that light that can form internal reflection is small and negligible. For the dual monochromator and the filter, and between the integrating sphere and the filter, the effect of this internal reflection on the measurement is due to the internal reflection characteristics of the integrating sphere and the small sphere opening relative to the integrating sphere. Very small, can be ignored. In summary, the internal reflection is small (about 10-5 orders of magnitude) relative to other uncertainties in the device, and the overall internal reflection effect is negligible. Based on the above uncertainty source analysis and nist's tn1297 comprehensive uncertainty formula, the formula is as follows: Since each uncertainty is not related, equation (8) is changed as follows: Filter is obtained according to equation (9) The comprehensive uncertainty of the sheet transmittance measurement is 5.859×10-3. Table 2 is the uncertainty source of the spectral transmittance of the filter and the comprehensive uncertainty. 4 Conclusion The high-resolution spectrophotometer is used to measure the transmittance of the filter. The spectral coverage is 380~1000nm, and the measurement uncertainty reaches 5.859×10-3. This fully automatic single-channel spectrophotometer features: an integrating sphere and a high-precision detector, and a filter and detector as the measuring unit. The biggest benefit of this type of measurement is that the filters and detectors are considered as a whole and are in line with actual use. At the same time, the uniform monochromatic light emitted by the integrating sphere is incident at the actual incident angle, thereby avoiding measurement errors caused by different incident angles. This error is mainly due to the drift of the center wavelength of the transmittance as a function of the angle of incidence. The design of the spectrophotometer proposed in this paper not only fully considers the actual use conditions of the filter, but also avoids the correction of the transmittance value in the later data processing, and also meets the requirements in the measurement accuracy. In addition, from the analysis of the uncertainty of this experiment, the main work in the future is how to improve the system repeatability of the dual monochromator, which is a key to improve the accuracy of the system test. Key words: high-precision spectrophotometer; transmittance; US instrumentation ; UV-1100; UV-1800
Dock Station Type C,7-Port USB Charging Station Dock,7-Port Charging Station,Type C USB HUB,7 in 1 USB HUB C Docking Station