Central issue:
This article refers to the address: http://
The working principle of LED and its advantages in automotive lighting
LED driver design and features in automotive lighting applications
LEDs are used in automotive lighting defects and solutions
solution:
LED driver design in automotive lighting applications
LED is a new and efficient semiconductor light source with advantages that other light sources can't match. The future is bright in the future of automotive lighting applications. LEDs can be combined into LED arrays in series, parallel, etc. to meet automotive lighting intensity requirements. In view of the LED's illuminating characteristics, the design and characteristics of the LED driver are discussed, and the current problems and solutions of the LED are briefly described.
1 Car lights and requirements
At present, cars are becoming more and more civilian, and have become the main means of transportation. The safety of driving has aroused widespread concern in society. According to incomplete statistics, the mileage of a car at night or under natural light accounts for 25% of the total mileage, while traffic accidents here account for 40% of the total accidents, and more than half of the casualties occur at night. . Therefore, the exterior lights and signal lights are the key components for safe driving of the car, and the following conditions must be met:
(1) The car illuminator lights up without delay, the response time is faster, giving the driver more reaction time.
(2) The illumination is strong, and the driver's field of vision is improved at night or when there is insufficient natural light, and the indication of the external signal light is stronger.
(3) High seismic resistance, high reliability, and avoid accidents caused by lighting failures.
(4) Energy saving, which can effectively reduce the emission of exhaust gas and protect the environment.
(5) Based on the increasingly fierce competition in automobile sales, the design of the lamp should be practical and beautiful.
2 LED becomes a new star in automotive lighting selection
2.1 How LEDs work
The LED is a special diode and is a semiconductor device in which a PN junction is formed by doping or the like. When the diode conduction condition is met, current flows through the LED, releasing energy in the form of light and heat. LED is a current-controlled current-type component, and its luminous intensity is mainly based on the magnitude of the current passed. When it is forward-conducting, its voltage drop is very high, and it has a certain fluctuation range.
Since LEDs do not have infrared and ultraviolet radiation, the energy consumed is almost all thermal energy except for conversion to light energy, and can only be transmitted in the form of heat conduction. Therefore, the junction temperature will gradually increase when the LED is in operation. While the LED is a device with a negative temperature coefficient, the current flowing through the LED will increase with increasing temperature, which creates a positive feedback, causing a further increase in junction temperature. If left uncontrolled, the LED will burn out. The thermal parameters of the LED are closely related to the junction temperature of the PN junction. The relationship between the dominant wavelength and temperature is as follows:
Mp(Tl) = m0(T0)+ 3Tg #0.1nm/°C
It can be seen from the above formula that whenever the junction temperature of the LED rises by 10 ° C, the dominant wavelength (which can be observed by the human eye) drifts to the long wave by 1 nm (1 nm = 10-9 m), resulting in a decrease in the brightness of the LED and a light decay. Therefore, if the individual LEDs are overheated, the uniformity of the LED array illumination will be deteriorated.
2.2 LED significant lighting advantages
LEDs are called new light sources because LEDs have the characteristics of point and solid-state light sources, so they have advantages that other lighting sources cannot match.
(1) The life of LED can reach 100,000 hours theoretically, and the actual life can reach more than 20,000 hours. It is more advantageous than the 1 000 hours of ordinary white light bulbs and 10,000 hours of daylight lamps. replace.
(2) No delay in lighting, faster response time. The LED's startup time is only a few tens of nanoseconds, and the startup time is much shorter than that of incandescent bulbs.
(3) In the case of high light intensity and low natural light visibility, the incidence of automobile accidents is greatly reduced; basically no radiation, belonging to the "green light source".
(4) LED has small footprint, simple structure and high shock resistance. Designers can change the lamp mode at will, so that the car can be diversified to meet different consumer needs.
(5) LED light source is much less affected by voltage changes than incandescent bulbs, showing excellent safety and reliability, while consuming 80% less energy than incandescent lamps with the same efficacy, very energy efficient.
Based on the above advantages, LED can be widely used in automotive lighting, but a single LED can not meet the requirements of automotive lighting intensity, and must be used in series, parallel or series-parallel to form an LED array, as shown in Figure 1.
2.3 LED driver design and features
LED drive methods can be used in resistor limiting, linear regulators and switching converters. The resistor current limiting scheme is suitable for low-efficiency applications, so the efficiency is extremely high, and this method is not used for automotive lighting with a wide input voltage range; the linear regulator is suitable for low current or the LED forward voltage drop is slightly lower than the power supply. In the case of voltage, but also the problem of low efficiency and small input voltage range; the switching converter has the characteristics of flexible circuit topology, high efficiency and wide input voltage. Therefore, after considering factors such as work efficiency, installation size, quiescent current, operating voltage, noise, and output regulation, the drive circuit mostly uses a switching converter. The switching converter topology is divided into Buck, Boost and Buck-Boos. At present, LED is applied to automotive lighting, and its driving power supply must be a lead-acid battery.
Because the input voltage range of the battery will vary greatly from the normal range, the drive circuit generally uses the Buck-Boost topology to meet the voltage requirements of the LED array. The DC gain of this circuit topology (the ratio of the output voltage to the input voltage) is related to the duty cycle D (the ratio of the turn-on time to the period in one switching cycle). When the battery voltage is lower than the voltage required by the LED, adjust D > 0.5 to put the circuit in the boost state; when the battery voltage is higher than the voltage required by the LED, adjust D < 0.5 to put the circuit in a step-down state. The LED is a current-controlled current-type component whose brightness is proportional to the current flowing through it. If the LED is not driven by a constant current, the current passing through will cause the brightness of the LED to change even if the voltage is constant. In order to ensure stable and reliable brightness, the LED needs a constant current to drive, and the ripple current needs to be controlled to an acceptable level under any circumstances. Therefore, the output of the LED driver circuit must be a constant current output rather than a constant voltage output.
The schematic diagram of the LED driver circuit can be designed as shown in Figure 1.
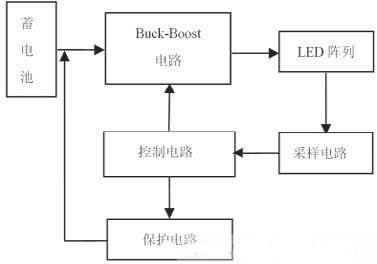
Figure 1 LED drive schematic
As can be seen from Figure 1, the Buck-Boost circuit converts the battery power and supplies power to the LED array. The sampling circuit samples the current flowing through the LED and transmits the signal to the control circuit. The control circuit analyzes the sampling information, adjusts the duty cycle of the switching tube in the Buck-Boost circuit, and ensures that the current through the LED is constant; when the circuit is abnormal, the power is cut off by the control protection circuit to ensure that the LED is not damaged. In general, the LED driver circuit must meet the following requirements:
(1) Lifting and lowering function. When the input voltage or the voltage drop of the LED itself fluctuates, the output voltage is adjusted to meet the requirement of constant output current to ensure stable and reliable LED illumination.
(2) High power conversion efficiency. To reduce drive losses, save costs, while reducing battery charging times and extending battery life.
(3) Brightness adjustment function. When the surrounding environment is very dark, the signal light often does not need to drive at the maximum current. At this time, the driving current can be controlled to change the brightness of the LED, thereby reducing the power consumption of the LED. A common method of adjusting the drive current is to use PWM signal control.
(4) It has a perfect protection circuit. Various protective measures should be provided to protect themselves and the LEDs from working reliably. For example, low voltage latching, overvoltage protection, overtemperature protection, output open or short circuit protection.
(5) Good heat dissipation. From the thermal characteristics of LEDs, temperature is one of the important factors affecting LED operation. When driving at night, the LED is on for a long time. Therefore, it must have a good heat dissipation function to ensure the life of the LED and reliable operation.
3 LED defects and solutions
3.1 Problems caused by inconsistency
In theory, LEDs are all light-emitting diodes, but the performance of individual LEDs in actual LED arrays is different due to differences in material purity, process and package (even by the same manufacturer). This will cause the LED's luminous intensity to be different from the driving current, and the difference between overcurrent resistance and heat generation will naturally be different. Because the LED difference always has a first damage, it will increase the current and damage other LEDs. This is the result of the inconsistency band and one of the factors that constrain its development. Therefore, manufacturers should improve the quality of LEDs to avoid large differences. At the same time, when designing the driver circuit, the corresponding protection circuit should be designed to prevent the above phenomenon.
3.2 The problem of complex drive circuit
First of all, in terms of voltage matching, LEDs are not like ordinary incandescent bulbs, and can be directly connected to 220V AC mains. The LED is a low voltage driver of 3.6 to 4.5V, and a complicated conversion circuit must be designed. Secondly, in terms of driving current, in order to ensure the normal operation of the LED, it is necessary to supply power to the constant current and constant voltage circuits, and to add a protection circuit. In this way, the power circuit complexity and failure rate will increase, which greatly limits the market competitiveness and purchase groups.
Therefore, the design should use a dedicated driver chip to simplify the structure of the driver circuit and enhance the stability of the system. For example, the FAN5608 series, CAT4201, LT3754 and other chips have a good effect on LED drivers.
3.3 LED cost issues
If a car is replaced with LEDs, about 200 to 300 LEDs are needed inside and outside. Compared with other lighting sources, the cost is quite high. Although the advantage of long life can make up for its high cost disadvantage, in general, its cost is still much higher than other light sources. This is the main reason why LED performance is outstanding but does not occupy a large market share.
However, governments attach great importance to LED technology and invest a lot of money every year to conduct research. I believe this issue will be satisfactorily resolved in the near future.
4 Conclusion
Due to the high cost of LEDs and the complexity of the drive technology, it has not yet fully entered the automotive market. China has already stipulated that all vehicles on the expressway must be equipped with LED fog lamps. In the future, as LED prices gradually decline, their lamp modules will gradually use high-brightness LEDs as light sources. Since the launch of Audi's first R8 with LED headlights, internationally renowned car companies such as Cadillac, BMW, Toyota, Mercedes-Benz and Ford have launched new cars with colorful LED lights to attract customers. With the continuous development of the automotive industry, LEDs will be widely used in the automotive market in the next few years. Overall, the LED lighting of automotive lamps is a major trend in the development of automotive lamps, and it will certainly be a leap in the history of the development of automotive lighting systems.
Smt Belt , original and new, in stock, quality guarantee, fast delivery.
SMT Belt is classified: motor belt, rail belt, head belt, timing belt, conveyor belt etc.
40000733 TIMING BELT YB(L) JUKI 2050 2055 2060 2070 2080 1070 1080 CX-1
40016697 TIMING BELT YB(E) JUKI 2050 2055 2060 2070 2080 1070 1080
40001143 TIMING BELT Z JUKI 2050 2055 2060 CX-1
40001116 TIMING BELT T JUKI 2050 2055 2060
40001160 TIMING BELT IC Z JUKI 2060
40000863 CONVEYOR BELT S JUKI 2050 2055 2060 2070 2080 1070 1080 2077
40000864 CONVEYOR BELT C JUKI 2050 2055 2060 2070 2080 1070 1080 2077
40001860 CONVEYOR BELT S(E) JUKI 2050 2055 2060 2070 2080 1070 1080 2077
40000790 CONVEYOR BELT EX(W) JUKI 2050 2055 2060 2070 2080
40001070 CONVEYOR BELT C(L) JUKI 2050 2055 2060 2070 2080 3020 1070 1080 2077
40000852 DRIVE BELT S JUKI 2050 2055 2060 2070 2080 3020 1070 1080 2077
40001005 DRIVE BELT C(L) JUKI 2050 2055 2060 2070 2080 3020 1070 1080 2077
E2155721000 DRIVE BELT C JUKI 2010 2010 2040 2050 2060 2070 2080 2070 2080 CX-1
Smt Machine Spare Parts
Original Smt Feeder
Original Smt Cable
Smt Machine Cable
Smt Spare Parts Fuji Cable
SMT Cable
Smt Belt
Smt Siemens Belt
Smt Juki Belt
Smt Conveyor Belt
Smt Camera
Smt Laser
Camera For Smt
Smt Siemens Camera
Smt Parts Plastic Rail
Smt Plastic Rail
Smt Juki Plastic Rail
Juki Plastic Rail
SMT Nozzle For Yamaha
Yamaha Nozzle
Nozzles For Yamaha Machine
Smt Yamaha Nozzle
Smt Siemens Nozzle
Smt Nozzle For Siemens
Siemens Nozzle
Smt Nozzle For Samsung
Samsung Nozzle
Smt Samsung Nozzle
Panasonic Nozzle
Smt Panasonic Nozzle
Smt Nozzle For Panasonics
Nozzles For Panasonic Machine
Smt Juki Nozzle
Nozzles For Juki Machine
Juki Nozzle
High Pressure Juki Nozzle
I-Pulse Nozzle
Nozzles For I-Pulsemachine
Smt I-Pulse Nozzle
High Pressure Fuji Nozzle
Nozzles For Fuji Machine
Fuji Nozzle
Smt Fuji Nozzle
Smt Nozzle
Smt Parts Nozzle
Smt Nozzle For Machine
Smt Spare Parts Nozzle
Yamaha Smt Feeder
Yamaha Feeder
Smt Machineyamahafeeder
Smt Feeder For Yamaha
Smt Feeder For Siemens
Smt Machine Siemens Feeder
Siemens Smt Feeder
SIEMENS Feeder
Samsung Smt Feeder
Smt Machine Samsung Feeder
SAMSUNG Feeder
Smt Feeder For Samsung
Panasonic Smt Feeder
Panasonic Feeder
Smt Machine Panasonic Feeder
SMT Feeder For Panasonic
Smt Feeder For Juki
JUKI Feeder
Juki Smt Feeder
Smt Machine Juki Feeder
I-Pulse Feeder
Smt I-Pulse Feeder
Smt Parts I-Pulse Feeder
I-Pulse Type Feeder
Pneumatic Feeder
Fuji Feeder
Smt Fuji Feeder
Fuji Smt Tape Feeder
Smt Machine Feeder
Smt Tape Feeder
Smt Feeder
Feeder For Smt Machine
Siemens Control Valves
Smt Siemens Valve
Siemens Vacuum Valve
Siemens Valves
Smt Samsung Valve
Samsung Vacuum Valve
Samsung Control Valves
SAMSUNG Valve
Juki Vacuum Valve
Juki Ejector
Juki Vacuum Ejector
Juki Valve
Ejector For Vacuum
Smt Vacuum Ejector
Smt Vacuum Valve
Cylinder For Samsung
Smt Samsung Cylinder
Samsung Air Cylinder
SAMSUNG Cylinder
Panasonic Pir Sensor
Panasonic Sunx Sensor
Panasonic Original Sensor
Panasonic Sensor
Juki Sensor
Juki Laser Sensor
Juki Smt Sensor
Laser Sensor
Juki Cylinder
Juki Square Cylinder
Juki Air Cylinder
Cylinder Square
SMT Belt
Smt Juki Belt,Smt Belt,Smt Conveyor Belt,Smt Siemens Belt
Shenzhen Srisung Technology Co.,Limited , https://www.sr-smt.com